Functional testing is crucial in the PCB assembly process, ensuring the final product performs its intended functions correctly. At OurPCB, functional testing is conducted meticulously to verify assembled PCBs’ electrical performance and reliability. This article delves into the intricacies of functional testing and its significance in the PCB assembly process.
Understanding Functional Testing in PCB Assembly
Functional testing involves simulating a PCB’s operational environment to check its performance. This process tests various functions of the PCB, including signal processing, power management, and communication interfaces. The objective is to identify faults or deviations from the desired performance specifications.
The Functional Testing Process
- Preparation: A comprehensive test plan is developed based on the PCB’s design and intended applications before testing. The test plan outlines the parameters to be tested, the testing methodology, and the acceptable performance criteria.
- Test Fixture Development: Custom test fixtures are created to interface with the PCB. These fixtures connect to the PCB’s test points and simulate the operational environment.
- Test Execution: The PCB is powered up, and various inputs are applied to simulate real-world conditions. Automated test equipment (ATE) runs predefined test sequences and records the PCB’s responses.
- Data Analysis: The test results are analyzed to identify any discrepancies. If the PCB fails any test, the root cause is investigated, and necessary corrective actions are taken.
- Report Generation: A detailed report is generated, documenting the test results and any corrective actions taken. This report serves as a quality assurance document for the PCB assembly.
Functional testing begins with a comprehensive test plan developed based on the PCB’s design and intended applications. The test plan outlines the parameters to be tested, the testing methodology, and the acceptable performance criteria.
Custom test fixtures are then created to interface with the PCB. These fixtures connect to the PCB’s test points and simulate the operational environment. The PCB is powered up, and various inputs are applied to simulate real-world conditions. Automated test equipment (ATE) runs predefined test sequences and records the PCB’s responses.
The test results are analyzed to identify any discrepancies. If the PCB fails any test, the root cause is investigated, and necessary corrective actions are taken. A detailed report documenting the test results and any corrective actions taken is generated. This report serves as a quality assurance document for the PCB assembly.
Importance of Functional Testing
Functional testing is essential for several reasons:
- Quality Assurance: Ensures that the PCB performs as intended, reducing the risk of field failures.
- Reliability: Identifies potential issues early in the manufacturing process, enhancing the reliability of the final product.
- Compliance: Verifies that the PCB meets industry standards and regulatory requirements.
- Customer Satisfaction: Delivers high-quality products that meet customer expectations, fostering trust and repeat business.
Advanced Techniques in Functional Testing
With technological advancements, functional testing has become more sophisticated. Techniques such as boundary scan testing, in-circuit testing (ICT), and automated optical inspection (AOI) are integrated with functional testing to comprehensively evaluate the PCB’s performance.
- Boundary Scan Testing: Uses standard test access ports to check the integrity of interconnections on the PCB.
- In-Circuit Testing (ICT): Checks individual components on the PCB to ensure they are correctly placed and functional.
- Automated Optical Inspection (AOI): Uses cameras and software to inspect the PCB for visual defects.
FAQs
Q1: What is the Primary Purpose of Functional Testing in PCB Assembly?
Functional testing’s primary purpose is to verify that the PCB operates correctly and meets the specified performance criteria.
Q2: How does Functional Testing Differ from In-circuit Testing (ICT)?
Functional testing evaluates the PCB’s overall performance in simulated operational conditions, while ICT checks individual components and their placement on the PCB.
Q3: What Equipment is used in Functional Testing?
Functional testing uses automated test equipment (ATE), custom test fixtures, and sometimes boundary scan testers.
Q4: Can Functional Testing Identify All Types of Defects in a PCB?
While functional testing is comprehensive, it may not identify all defects.
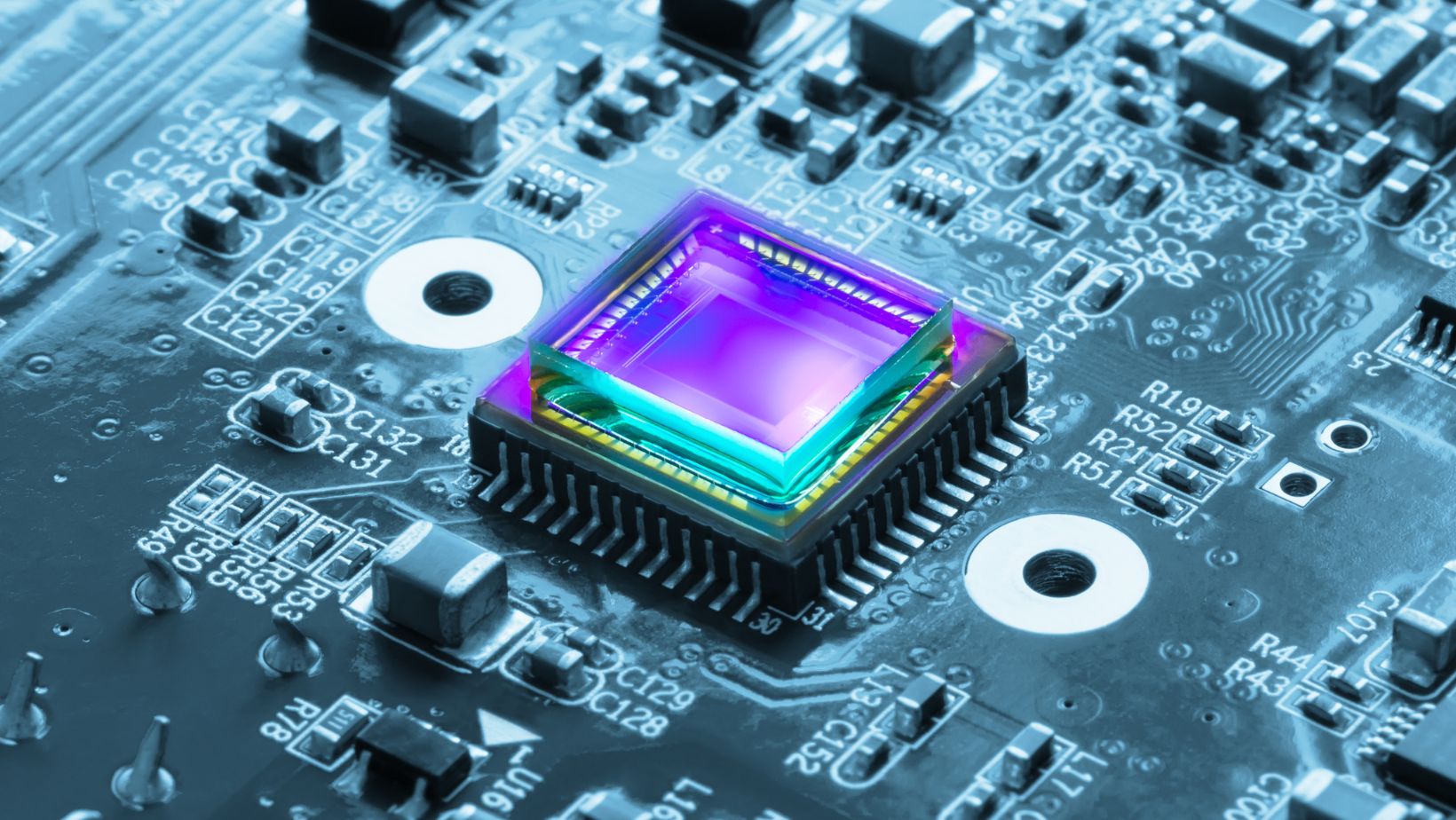
It is often combined with other testing methods like ICT and AOI for thorough inspection.
Q5: How Important is Functional Testing for High-reliability PCBs?
Functional testing is critical for high-reliability PCBs, especially in industries like aerospace and medical devices, where performance and reliability are paramount.